ADVANTAGEOUS PRODUCTS AND APPLICATION FIELDS
Non-woven fabric/dust bag – mainly used in the field of solid-gas separation: electric power, steel, metallurgy, cement, chemical industry, waste incineration, etc.
Woven cloth/filter bag – mainly used in the field of solid-liquid separation: sewage treatment, chemical industry, food, metallurgy, medicine, electronics, etc.;
MAIN RAW MATERIALS
High-temperature filter material: It has passed the testing standards of the European Union and the United States for many years, and has become a major supplier. Especially in the United States, the application of PPS and MX series products has always been in the forefront of the industry; other aramid fibers, polyimide, glass fiber, chlorine Fiber, PTFE, etc.
Room temperature material: polyester, polypropylene, nylon, vinylon, PBT, acrylic;
Multi-material composite filter media: It is the key direction, especially PPS and PTFE composite filter media have excellent performance.
Film-coated filter materials: Based on the strength of Yan brand filter equipment, the cost-effectiveness of film-coated filter materials is obvious, including glass fiber coating. Using American PPG 6um yarn to make acid-proof glass fiber woven fabric in Korea KPI, and make Yan brand high-performance glass fiber membrane filter material;
COOPERATIVE USERS ARE HIGHLY RECOGNIZED
In the long-term development process of Yanpai, it has gradually gained the support of mainstream users in the industry, and they have been helping Yanpai’s products to be applied in various industries. Yanpai Co., Ltd. attaches great importance to the communication and collaboration with partners, and constantly accumulates application experience, innovates products, and improves service system.
ALUMINA INDUSTRY
Yanpai Co., Ltd. can tailor-made filter cloths for alumina enterprises. The filter cloth produced by the company is widely used in all processes such as red mud separation, crude liquid separation, crystal seed washing, chemical alumina, etc. in the alumina industry, and is suitable for rotary drum machines, belt filters, vertical leaf Filters, horizontal leaf filters, turntables, flatteners, and all other models.
Special filter cloth for leaf filter:
The special filter cloth of Yan brand alumina leaf filter is made of imported raw materials, high temperature setting and calendering treatment, uniform mesh, stable air permeability and smooth surface. The size standard of the filter bag of the leaf filter is fine and the workmanship is fine. If the equipment is in good condition, the service life can reach 3 months, and the suspended matter can reach below 5mg/L within five minutes.
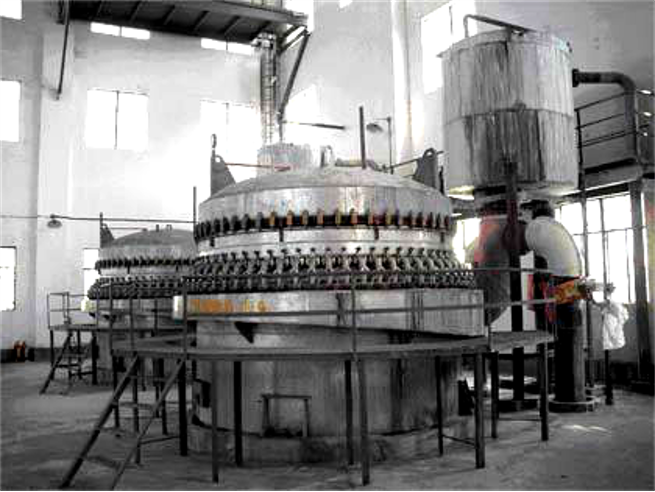
Leaf filter working conditions:
Each filter needs to handle the minimum liquid flow: 510m3/h
Maximum feed solid content: 300-600mg/l
Caustic alkali concentration (expressed as Na2Ok): 165-175g/l
AL2O3 concentration: 188g- 195g/l
The concentration of Na2CO3 in terms of Na2Ok: 20g/l
Cl concentration: 12g/l
Liquid temperature: 105℃
Solid content of filtered material: 15mg/l
Special filter cloth for vertical disc filter:
Yan brand alumina vertical disc filter special filter cloth, the service life is generally 1800-2000 hours. Now we provide professional customized services for domestic alumina plants, which can be adjusted according to actual working conditions.
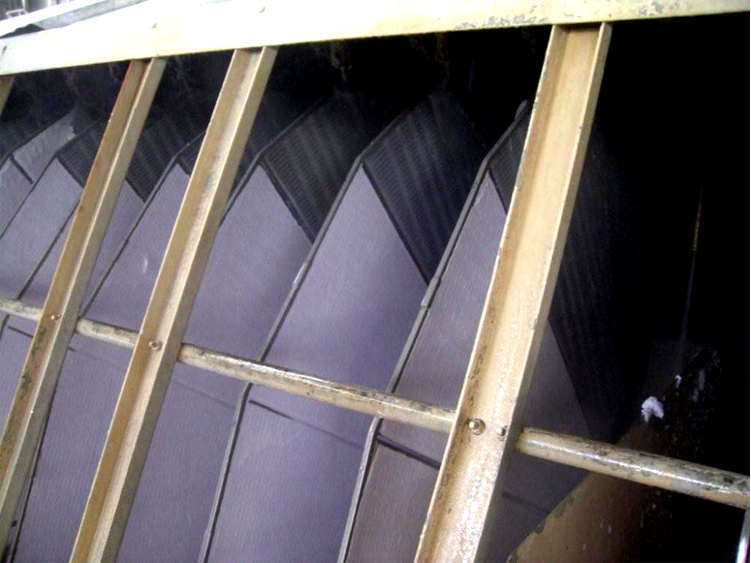
Vertical disc filter working conditions:
Filter Media: Aluminum Hydroxide
Slurry solid content: 700~1200g/L
Slurry Nk concentration: 160~200g/L (aluminum hydroxide)
Back blowing pressure: 0.1MPa≤P≤0.6MPa
Operating temperature: 42~50℃
Operation mode: indoor, continuous operation
Vacuum degree: ≤-0.025MPa
Special filter cloth for flat disc filter:
Yan brand alumina flat disc filter special filter cloth, used on the finished alumina flat disc filter, the service life is generally about 2 months. The suspended matter is less than 0.7g-4g/L, and the drying rate of the filter cake is about 4%-8%.
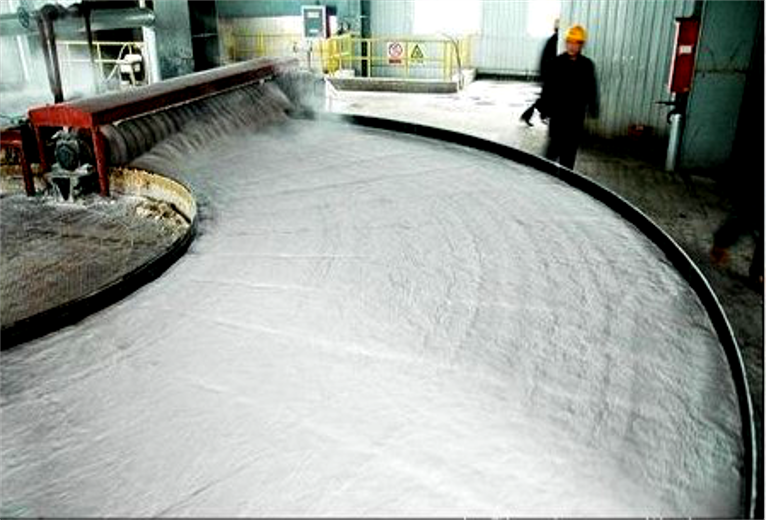
Working conditions of flat disc filter:
Working medium: lye (aluminum hydroxide slurry, filtrate), hot water
Working temperature: -30℃-150℃
Vacuum degree, back blowing pressure: 0.03-0.06MPa
Alkali concentration: 0-320g/L
Slurry flow: 0-180m³/h
Red mud washing:
The settled red mud is still highly viscous, and it is difficult to separate the solid and liquid during the washing process, and it is also difficult to separate from the filter medium.
Traditional filtration machines include box-type filter presses. It is very difficult to wash a single filter cloth. Now most of them use spinning filters. Some spinning filters use an external roller to remove the filter cake. The effect of washing and separation is ideal. The manufacturer uses a horizontal vacuum belt filter, but the effect is not ideal.
Filter cloth recommendation:
In the selection of filter cloth, most of them are monofilament polypropylene filter cloth, and the mesh size is about 30-50um. Yanpai Co., Ltd. and the main alumina manufacturer research institutions have developed and successfully tested the 2815 series monofilament filter cloth. This filter cloth can improve the use effect of the filter cloth on the spinning machine by modifying the process.
Advantage:
The advantages of this kind of polypropylene filter cloth: the uniform and smooth monofilament makes the filter cloth have better mesh stability and cake removal, which not only ensures the quality of the product, but also maximizes the washing effect.
Seed Wash:
The decomposed aluminate solution is separated from the aluminum hydroxide solution in the concentration, the obtained aluminum hydroxide is classified in the classification machine, the fine aluminum hydroxide is returned as the particle to decompose the sodium chlorate solution, and the large part is washed and filtered. Then choose to calcine,
Vertical disc filters are used as filters for seed washing, and vacuum belt filters are also used.
Filter cloth recommendation:
In the selection of filter cloth, monofilament filter cloth or non-woven fabric is generally used. The materials are polypropylene and polyamide. The mesh size of the filter cloth used is 50-60um.
Advantage:
This type of filter cloth has good wear resistance, strong regeneration performance, and a long service life of about 1800 hours, which greatly reduces the downtime caused by replacing the filter cloth.
COAL WASHING INDUSTRY
Yanpai Co., Ltd. can customize the required filter cloth for users in the coal washing industry. The filter cloth produced by the company is widely used in various physical separation and filtration process sections in the coal washing industry, and is suitable for drum machines, belt filters, vertical leaf filters, and horizontal leaf filters in related industries including coal washing plants. Machines, flipping machines, flattening machines, and all other models.
The main product types of our filter cloth:
The filter cloth is the heart of the filter press. The quality of the filter press fabric directly affects the filtering effect of the filter press. Moreover, both filter cloth and processing level are indispensable. Our filter press filter cloth is mainly medium and thick fabric, including polyester, polypropylene and other materials, monofilament filter cloth, imported double-layer filter cloth, etc., and has an independent high-quality processing workshop, and according to the fineness of the material , the company launched 400 mesh, 800 mesh, 2000 mesh and other monofilament filter cloths to meet the various filtration precision requirements of the coal washing industry.
Our product advantages
Filter cloth processing: According to the size and special requirements of each customer, such as brushed filter cloth, embedded filter cloth, hanging filter cloth, plate and frame filter cloth, filter cloth hemming, filter cloth punching, etc., you can come Sample processing to drawings.
Filter cloth application: widely used in chemical, metallurgy, petrochemical, pharmaceutical, food, mining, coal, ceramics, environmental protection and other fields, suitable for various types of filter presses such as plate and frame, box type, diaphragm, etc.
Use effect: 1. Improve productivity and reduce cycle time; 2. Remarkably improve cake removal effect; 3. Effectively reduce cleaning frequency; 4. Clear filtrate; 5. Dry filter cake, very good labor efficiency.
Selection basis:
A. The peeling performance of the filter residue: it directly affects the working efficiency of the filter press equipment. The surface of the filter residue is smooth and non-adhesive, and the filtrate will quickly seep out from the filter cloth. The filtration time is short and the efficiency is high. On the contrary, the filter residue is sticky, and the filtration time will be long, and the efficiency will of course be reduced accordingly. And the stronger the adhesion, the lower the efficiency. At this time, we will choose monofilament filter cloth or satin weave filter cloth.
B. According to the acidity and alkalinity of the filtrate: choose the type of filter cloth that suits you according to the acidity and alkalinity. The stronger acid resistance is polyester filter cloth, and the stronger alkali resistance is the vinylon filter cloth. Polypropylene filter cloth is also resistant to acid and alkali.
C. Wear resistance of filter material: Whether the shape of the filter residue, whether the particles are uniform, and whether the shape is hard, consider the wear resistance of the filter cloth. The size is uneven, and there are edges and corners, which are selected according to the different degrees. The ones with better wear resistance are polyester filter cloth and nylon filter cloth.
Yan brand special filter cloth for coal washing industry:
Yan brand special filter cloth for coal washing industry is generally used in filter presses in coal washing plants. Working conditions (for reference): Alkali concentration: 0-320g/L Slurry flow: 0-180m³/h
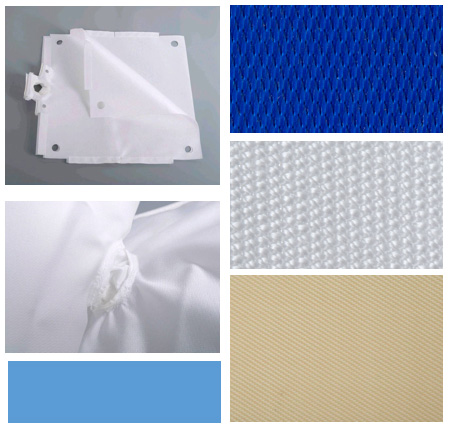
Recommended model:
Material: Nylon PA
Model: PA1422/PA1426 (monofilament filter cloth)
Air permeability: 1000L/㎡/s
product features:
1. Excellent acid and alkali resistance and high tensile strength.
2. After shaping treatment, it is smooth and flat, with better air permeability and water permeability.
3. Tough and durable, the filter cake is easy to peel off and easy to regenerate.
4. The interface is sewn with acid and alkali resistant high-strength thread, which is durable.
POWER INDUSTRY
In order to ensure that the project meets the emission requirements of 10 mg, Yanpai uses high-precision filter materials independently developed and designed to make filter bags, which can ensure the ultra-low emission requirements. Technical experts carry out fine management of the whole process.
PPS+PTFE dust bag:
Features:
The base fabric and the front/back surface are all 100% PPS material;
PTFE+PPS is composed of front/back dust surface, which greatly improves chemical performance and is suitable for highly corrosive working conditions; it is composed of PTFE base cloth + PPS front/back dust surface in the middle to improve chemical resistance, usually in coal containing Slightly high sulfur content

Applicable working conditions:
• Especially suitable for processes with high emission concentration requirements
• Flue gas purification for cement kilns, drying, combustion, smelting, and asphalt mixing;
• Flue gas purification of various industrial kilns and coal-fired boilers;
• Flue gas purification of some waste incineration, etc.;
PTFPTF E – PTFE Dust Bag:

Applicable working conditions:
• Suitable for harsh conditions where corrosion resistance is required, and where the service life of the filter material is high
• Waste incineration, carbon black production, titanium dioxide (Ti O 2 ) production process;
• The primary smelting, refining and chemical production processes of some metals;
Features:
Under the condition of continuous operation at 240°C and instantaneous temperature of 260°C, it can withstand all
Acid-base attack in the pH range; therefore, often blended with other materials to improve filter media
chemical resistance;
STEEL INDUSTRY
In order to ensure that the project meets the emission requirements of 10 mg, Yanpai uses high-precision filter materials independently developed and designed to make filter bags, which can ensure the ultra-low emission requirements. Technical experts carry out fine management of the whole process.
Ultra-low emissions in the steel industry:
Dust removal in the iron and steel industry has always been the traditional advantage of Yanpai Co., Ltd.: For dust removal in the normal temperature section, Yanpai Co., Ltd.
And the membrane filter material, in the filtering wind speed within 0.8m/min, the discharge is basically below 5mg, and maintains a low and stable pressure difference;
Sintering machine semi-dry desulfurization and dust removal:
According to the dry high-concentration dust conditions, Yanpai Co., Ltd. uses the PPS microfiber surface layer filter material to make the filter material through fine processing such as bag head sewing and seam coating silica gel.
Bags, professional installers are responsible for the combined process construction process to meet high emission requirements;
Dust control points in iron and steel industry:
From mining, crushing, screening, transfer, coking, sintering, blast furnace smelting, converter steelmaking, electric furnace steelmaking, steelmaking auxiliary raw material systems, molten steel refining, slab cutting
A large amount of dust and smoke are generated in the production process of the whole process (including flame cleaning) to hot rolling and cold rolling;
Dedusting of blast furnace and converter raw material systems:
A large amount of dust is generated in the process of transportation, screening, storage, and feeding, and the dust composition is diverse, such as pellets, sintered ore, miscellaneous ore, coke powder, coal powder, clay, ferroalloy and lime, etc., which belong to normal temperature conditions. .
Dust concentration: about 5 g/Nm3~15 g/Nm3.
Filter material scheme: PE is the base material, and anti-static, oil-proof and water-proof, film coating and other processes can be selected according to particle size and working conditions.
Dust removal in blast furnace casting yard:
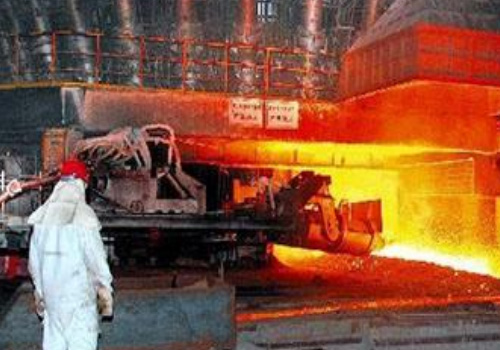
When the blast furnace is tapping, a large amount of dusty flue gas is generated in the tap hole, main trench, slag skimmer, slag trench, and molten iron tank.
Flue gas temperature: 60℃~100℃
Dust concentration: 5 g/Nm3~15 g/Nm3
50% particle size: 5 µm to 10 µm
Filter material scheme: 550 grams of PE film, 650 grams of PE filter material.
Converter secondary dust removal:
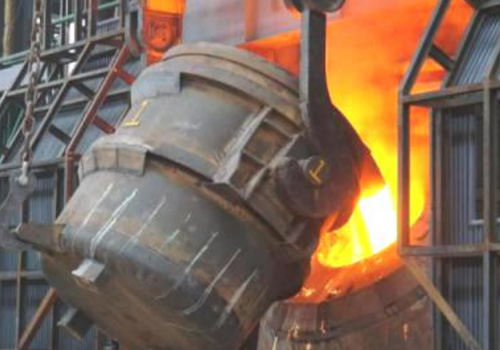
The converter produces a large amount of secondary flue gas during the process of mixing molten iron, adding scrap steel, tapping and converter blowing, etc.
The dust is essentially an oxide of iron.
Flue gas temperature: 60℃~130℃
Dust concentration: 2g/Nm3~5g/Nm3
Filter material scheme: 550 grams of PE filter material, 550 grams of PE film, PE microfiber filter material.
Steelmaking electric furnace dust removal:
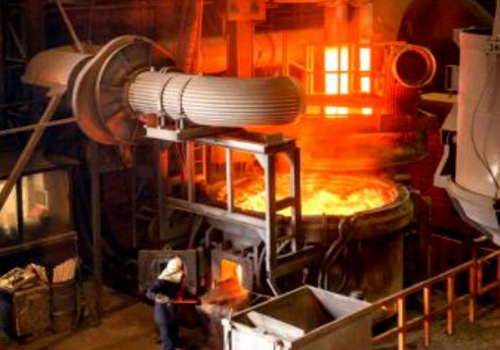
The steelmaking electric furnace produces a large amount of flue gas during the smelting process; the main characteristics of the working conditions are the large amount of flue gas and the fine dust particles; almost 100% of them are below 5 μm to 10 μm, and the viscosity is large.
Flue gas temperature: <130℃
Dust concentration: 8g/Nm3~15g/Nm3
Filter material scheme: 650 grams of PE filter material, 650 grams of PE film coated filter material, 550 grams of PE film coated, PE ultrafine fiber filter material.
Dedusting of blast furnace and converter raw material systems:
A large amount of dust is generated in the process of transportation, screening, storage, and feeding, and the dust composition is diverse, such as pellets, sintered ore, miscellaneous ore, coke powder, coal powder, clay, ferroalloy and lime, etc., which belong to normal temperature conditions. .
Dust concentration: about 5 g/Nm3~15 g/Nm3.
Filter material scheme: PE is the base material, and anti-static, oil-proof and water-proof, film coating and other processes can be selected according to particle size and working conditions.
Converter + blast furnace gas power generation and dust removal:
After the surplus gas is burned for power generation, the exhaust gas has the characteristics of relatively stable working conditions, low flue gas corrosion, low dust content, and low flue gas temperature.
Filter material scheme: PPS550g should be used; the filtering wind speed is less than 0.75m/mi.
Sintering flue gas dust removal:
Nose smoke
Dust is mineral powder, coke, etc.; contains harmful gases such as SO 2 and NO X, dust
Strong abrasiveness, high humidity, strong corrosiveness; cold water is produced from cold state to hot state;
Electrostatic precipitator + wet desulfurization is changed to semi-dry desulfurization + cloth bag.
Filter scheme: 100%PPS, PPS/TF, PPS+TF/TF.
Tail smoke
The working condition of unloading flue gas is relatively simple, and the selection of filter material is mainly based on temperature.
Mixed flue gas dust concentration: 5-15g/Nm3, unmixed dust concentration is lower
Flue gas temperature: 60~180 ℃
Filter material scheme: PE, acrylic (DT), DT composite, PI composite felt, etc.
CEMENT INDUSTRY
Yanpai Co., Ltd. has cultivated earlier in the cement industry and has a more complete product chain; all kinds of filter materials such as normal temperature, high temperature, chemical fiber, glass fiber are readily available; at the same time, Yanpai is also the best domestic manufacturer of breathable layer cloth; its advantageous products There are MX, PI, GL-11, etc.
Yan brand unique – breathable layer cloth: the breathable layer cloth is suitable for the air chute of the cement plant grinding station, the air box homogenization storehouse cement pneumatic conveying, and the homogenization storehouse. It is an indispensable accessory product in the cement industry.
Cement mill dust removal:
Cement mill dust removal is divided into raw meal mill and clinker mill. Under the original emission standard, PE550 grams of conventional filter material is basically used, which is oil-proof and waterproof.
Imported flue gas dust concentration: usually ≤ 300g/m3
Flue gas temperature: less than 120 ℃
Filter solution: for ≤10mg/Nm3 ultra-low emission transformation, push
The recommended filter material is PE ultra-fine blended surface layer 550g filter material, oil-proof, anti-oil
Water treatment; it is recommended that the filtration wind speed be less than 0.75m/min.
Coal mill dust removal:
At present, in the new dry process cement production line, the original PE 550 gram conventional filter material is basically used, with anti-static, oil-proof and waterproof treatment;
Coal mill exhaust gas temperature: generally 60 ~ 80 ℃
Flue gas pulverized coal concentration: generally can reach 600~800g/m3
Particle size: less than 10μm accounts for 40%~80%
Filter material scheme: for ≤ 10 mg / N m 3 ultra-low emission transformation, recommended
The filter material is PE ultra-fine blended surface layer 550g filter material, 550g film coating, anti-static, oil-proof, waterproof treatment; it is recommended that the filtration wind speed be less than 0.75m/min;
Kiln head and kiln tail dust removal:
kiln head
Temperature: 150 ℃~200 ℃
Dust concentration: ≤30g/Nm3
Recommended filter media: MX550g filter media, PI+MX composite filter media;
Filtering wind speed: ≤ 0.75m/min;
Kiln tail
Temperature: 200~240℃, 150-180℃ after waste heat power generation
Dust concentration: ≤100g/Nm3
Filter material recommendation: PI/TF550g filter material, PI+MX composite filter material, glass fiber coating;
Filtering wind speed: ≤ 0.75m/min;
WASTE INCINERATION INDUSTRY
On March 28, 2019, Yanpai Co., Ltd. signed a school-enterprise strategic cooperation agreement with Zhejiang University, and established the “Environmental Catalytic Filtration Technology Research Center”, which was established by Zhejiang University.
The company is responsible for management, and has set up a post-doctoral workstation in Yanpai Co., Ltd. to organize waste incineration and disposal, environmental protection catalysis new materials,
R&D and industrialization of air filtration technology, dioxin and other pollutants synergistic removal technology;
The main research and development direction: on the basis of common filter materials, the collaborative treatment of dioxins and NOX multi-functional filter materials is attached;
Commonly used filter material solutions: 100% PTFE, 100% PTFE film, PTFE+PPS composite filter material, special acid-proof glass fiber film filter material
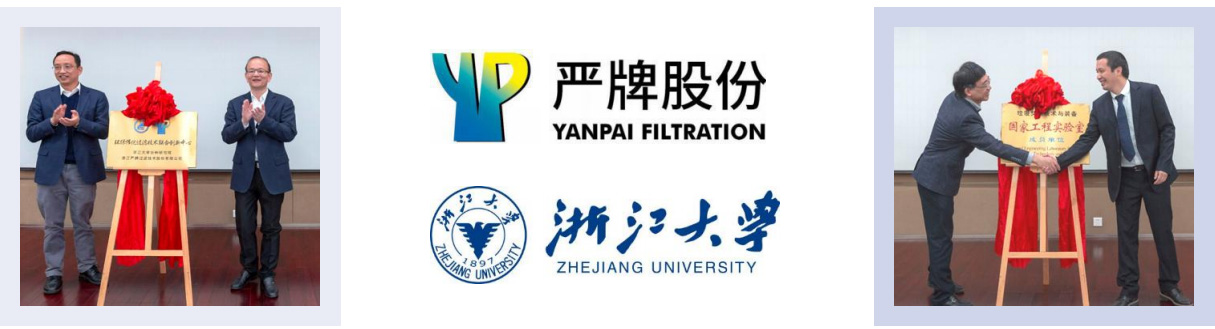